Naila Hfaiedh, presented the paper entitled “Fatigue life prediction of the AA2024-T351 aluminum alloy” at the 15th International Conference on Fracture (ICF15) in Atlanta, which took place in mid-June.
Naila Hfaiedh’s study proposes to investigate the cyclic behavior of the AA2024-T351 aluminum alloy, widely used in the aircraft industry.
Held every 4 years, the International Conference on Fracture is a must-attend event for senior and young researchers, students, post-doctoral fellows, and industry professionals working in fracture worldwide.
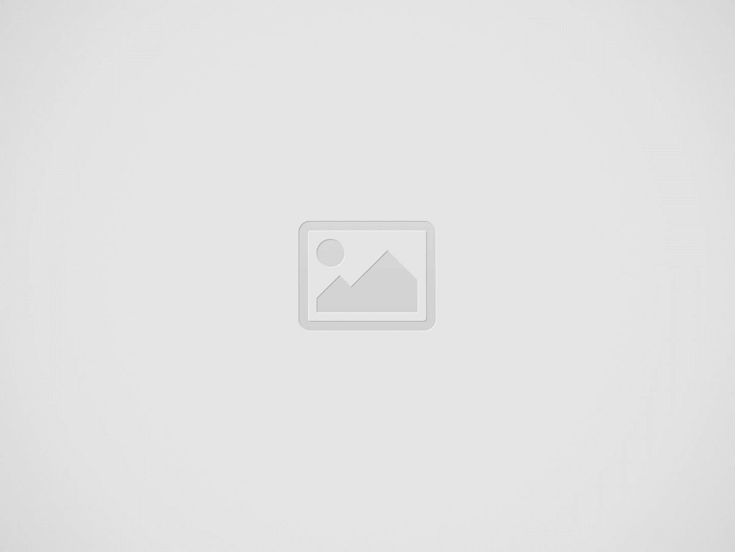
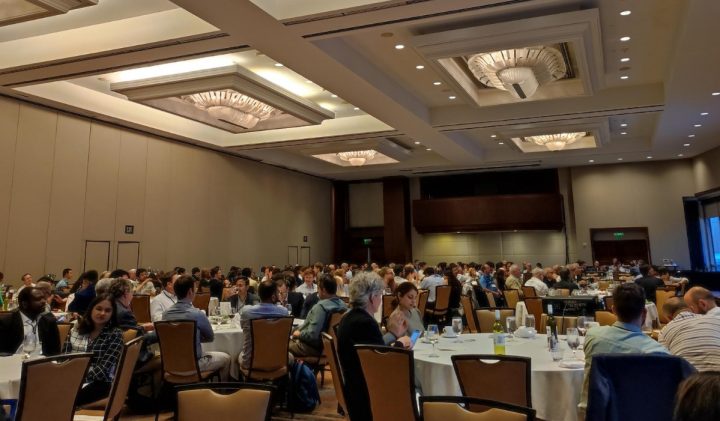
Researchers attending the conferences
Investigating the cyclic behavior of the aluminum alloy
This alloy shows a relatively low ductility at room temperature and is generally heat treated in various conditions to suit particular applications.
Monotonic and cyclic tests have been conducted in order to characterize the fatigue behavior and determine the fatigue life of aluminum alloy.
Cyclic tests in the Low Cycle Fatigue (LCF) regime were performed under fully reversed total strain amplitudes ranging between 0.6% and 1.2%. The elastoplastic behavior was analyzed through the stress-strain hysteresis loops leading to evaluate kinematic and isotropic hardenings. The AA2024-T351 was also shown to be prone to cyclic strain hardening.
Besides, symmetric High Cycle Fatigue (HCF) tests were also performed, and the Stress-Number of cycles (S-N) curve until 107 cycles were plotted. A fatigue limit of about 150 MPa was found.
Based on all LCF and HCF tests, the fatigue life could be represented in a strain approach by the Manson-Coffin-Basquin law. Moreover, observations of the fracture surfaces were carried out using a Scanning Electron Microscope (SEM) in order to detect the crack initiation and follow the propagation for the two fatigue regimes.
Aluminum alloy in the aeronautical industries
The aeronautical industries always demand innovation in, particular in the materials domain, by designing alloys with improved mechanical properties.
Aluminum-Copper alloys, and especially the AA2024-T351 aluminum alloy, have been used in aircraft components such as the wings and fuselage skins for more than 80 years, thanks to their good properties. Fatigue of materials is the process of accumulated damage and then failure due to cyclic loading.
Engineering efforts over more than 150 years aimed at preventing fatigue failure led first to the development of a stress-based approach. This approach emphasizes stress versus life curves.
More sophisticated approaches, namely the strain-based approach, have arisen in recent years. Stress versus life (S-N) curves are commonly plotted in terms of stress amplitude versus cycles to failure.
To understand the fatigue evolution, the Wohler curve will be studied. The microstructural analyses with SEM of the fracture facies of certain specimens allowed us first to conclude that the type of fracture in our material is ductile and to confirm the cracking modes obtained during cyclic loading.
The 5th International Conference on Fracture (ICF15) venue
The origin of fatigue damage in aluminum alloy
This work allows us to investigate the fatigue behavior of the AA2024-T351 aluminum alloy by estimating the fatigue life using stress approaches, cyclic tests in the Low Cycle Fatigue (LCF) and High Cycle Fatigue (HCF) regimes were studied, limited fatigue endurance was determined which is near 150 MPa.
Indeed, as depicted in Fig.2, a fatigue limit does appear on the S-N curve from about 106 cycles. It is also well known that aluminum alloys hardened by strain aging clearly exhibit a fatigue limit.
Finally, microstructural analyzes of the fracture facies allowed us to confirm that the fatigue damage originates from the surface and the type of fracture is ductile.
Learn more about ESILV’s programmes
This post was last modified on 28 November 2023 12:13 pm